
ROBOTIC PALLETIZER
A robotic palletizer is a machine designed to automate the process of stacking and arranging goods or products onto pallets for storage, transport, or distribution. Palletizing is a crucial step in various industries, including manufacturing, warehousing, and logistics, as it helps improve efficiency, reduce labor costs, and enhance overall productivity.
A robotic palletizer is an automated system designed to handle the palletizing process, which involves stacking and arranging goods or products onto pallets for storage, transportation, or distribution. These machines use robotic arms equipped with end-of-arm tools (EOAT) to efficiently and accurately pick up products from a conveyor or other source and place them onto pallets in a predetermined pattern
Robotic palletizers come with various features and capabilities designed to enhance efficiency, flexibility, and safety in the palletizing process. Here are some key features commonly found in robotic palletizer systems:
FEATURES:
-
Multi-axis movement for precise positioning.
-
Payload capacity is suitable for handling different product weights.
-
Programmable motion profiles for optimized movement.
-
Customizable grippers for handling various product types and sizes.
-
Quick-change capabilities for efficient tool switching.
-
Intuitive user interface for easy programming and operation.
-
Simulation tools for testing and visualizing palletizing sequences.
-
Cameras and sensors for product identification and location.
-
Object recognition for adapting to different product shapes and orientations.
-
Collision detection to prevent accidents and damage.
-
Emergency stop buttons and safety systems for rapid shutdown.

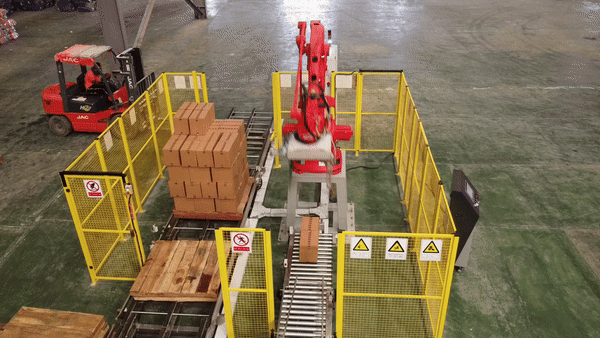


Eco-Friendly Design
Advantages:
-
Higher Speeds: Robotic palletizers can work at high speeds, significantly increasing the palletizing process's overall throughput compared to manual methods.
-
Consistent Performance: Robots maintain a consistent level of performance, reducing the risk of errors and ensuring uniform palletizing.
-
Automation of Labor-Intensive Tasks: Robotic palletizers eliminate the need for manual labor in the palletizing process, reducing labor costs and minimizing the risk of injuries associated with repetitive tasks.
-
24/7 Operation: Robots can work continuously, enabling 24/7 operation without the need for breaks or shifts.
-
Adaptability to Various Products: Robotic palletizers can be easily reprogrammed and equipped with different end-of-arm tools to handle a wide range of products, sizes, and shapes.
-
Quick Changeovers: Some systems allow for quick and easy changeovers between different palletizing tasks, making them suitable for diverse production lines.
-
Precision and Accuracy: Robotic palletizers can precisely place products on pallets, minimizing the risk of damage during the handling and stacking process.
-
Gentle Product Handling: The end-of-arm tools and gripping mechanisms can be designed to handle fragile or sensitive products without causing harm.
-
Compact Design: Robotic palletizers are often designed with a small footprint, making them suitable for facilities with limited space.
-
Flexible Layout: Their compact design allows for more flexible layout options within the production or warehouse space.
-
Versatility: Robotic palletizers can be programmed to create various palletizing patterns and configurations to meet specific packaging and storage requirements.
-
Ease of Reprogramming: Operators can easily reprogram the robots to adapt to changes in product types or stacking patterns.
-
Collision Avoidance: Robotic palletizers are equipped with sensors and systems to detect obstacles, preventing collisions and ensuring a safe working environment.
Robotic palletizers have emerged as a transformative solution for industries looking to streamline and optimize their palletizing processes. These automated systems bring a multitude of advantages, foremost among them being a significant boost in operational efficiency. With the ability to operate at high speeds and maintain consistent performance, robotic palletizers outpace traditional manual methods, leading to a substantial increase in overall throughput. Simultaneously, the adoption of these machines translates into substantial labor cost reduction, as they automate labor-intensive tasks, eliminating the need for manual intervention and minimizing the associated risks of repetitive work.
Flexibility in product handling is another hallmark of robotic palletizers. Their adaptability to various products, sizes, and shapes is achieved through customizable end-of-arm tools and the capability for quick changeovers. This flexibility ensures that these systems can seamlessly integrate into diverse production lines, catering to a wide range of product types. Moreover, precise and accurate product placement by robotic arms minimizes the risk of product damage during handling and stacking, contributing to improved overall product quality.
In terms of safety, robotic palletizers incorporate advanced features such as collision avoidance sensors and emergency stop functionalities. These ensure a secure working environment, mitigating potential risks and enhancing workplace safety. The compact design of robotic palletizers not only makes them suitable for facilities with limited space but also allows for more efficient use of available areas. Additionally, their compatibility with conveyor systems and seamless integration with automation and warehouse management systems contribute to a streamlined material flow and enhanced overall operational efficiency.
As industries increasingly recognize the need for modernization and automation, robotic palletizers stand out as a valuable investment. Their combination of increased efficiency, labor cost reduction, flexibility in product handling, and improved safety makes them a strategic choice for companies seeking to optimize their palletizing processes and stay competitive in today's dynamic business landscape.