
DRUM DECANTING UNIT (DDU)
DRUM DECANTING UNIT (DDU) FOR LUBRICANT ADDITIVES
Drum Decanting Units (DDUs) are mechanised and automated solutions for introducing small-volume additives into blends. These units have conveyor belts, load cells, control systems, rinse tanks, and swivel lances. Drum Decanting Units contribute to heightened efficiency and safety. The DDU is meticulously engineered for pumping and precisely dosing highly viscous liquids from drums, seamlessly integrating them into formulation processes. This technology is recommended for scenarios demanding the utmost accuracy in dosing and repeatability.
The Drum Decanting Unit (DDU) is not only a high-performance tool but also a user-friendly and safe solution. It can be used for emptying a defined value of additives without any cross-contamination into the production process of lubricants. The product's various operational features, such as decanting operation, rinsing operation, drum tilting, and heating, are designed for ease of use. The DDU brings the expensive additive into the production process without product loss, waste oil onset, and high-precision dosing by weighing technology. It satisfies the highest safety standards and runs in clean and completely closed conditions.
As a leading provider of industrial solutions, LINUS PROJECTS(INDIA) offers the Drum Decanting Unit (DDU) as a key tool for emptying a defined value of additives without any cross-contamination into the production process of lubricants.
The product has various operational features, such as decanting, Rinsing, drum tilting, and heating.
The high-performance DDU brings the expensive additive into the production process without product loss, waste oil onset, and high-precision dosing by weighing technology. The unit is easy to handle, satisfies the highest safety standards, and runs in clean and completely closed conditions.
Operation of DDU
A typical DDU uses roller conveyors to feed and discharge the drums or totes - one at a time - onto the drum-weighing platform.
FEATURES:
-
The proper drum is selected and fed in sequence onto the platform by the operator.
-
The platform is mounted on compression load cells that weigh the amount of each material and a tilting device is included to ensure maximum product recovery and removal.
-
In addition, a suction telescopic Nozzle using a flexible hose is inserted into the drum to withdraw liquid.
-
A screw Pump is provided to suck the oil and transfer it to the dosing or blending system.
-
The operator initiates production using the supervisory Control System which pulls and verifies the component recipe and line up.
-
When the set amount of material has been withdrawn from each drum, the lance is removed cleaned in a rinsing tube and restored for the next drum in sequence.
-
A rinse tank equipped with a heating system is included.
-
System flushes the nozzle and drum to remove any remaining material for maximum product recovery and minimum waste or cross-contamination.
-
Additionally, each empty drum is rinsed with a low viscosity component to minimize any residual material in the drum or tote.
-
A separate hose with quick-release coupling is provided to add the finishing oil from any system at a particular time.
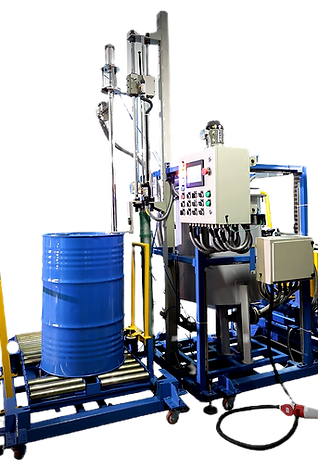


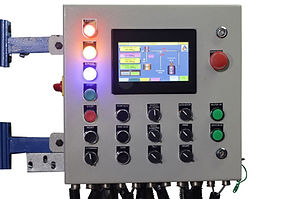
Advantages of our Drum Decanting Unit:
FEATURES:
-
Exact, reliable, and reproducible dosing of additives in the production process
-
Saving additives by emptying the drums.
-
No waste oil in the production process
-
No cross-contamination by cleaning the drum by hot rinse oil.
FEATURES AND BENEFITS OF OUR DDU
-
Eliminate manual dosing, cleaning, and overtreating for safer, efficient operations with the fully automated system including Clean-In-Place technologies
-
Maximize product recovery and removal with tilting devices to empty drums.
-
Increase flexibility by accommodating additives with a wide viscosity range or by adding components manually if required by the recipe.
-
Avoid over-treating through accurate dosing
-
measure setto computention of the decanting operation.
-
Directly blend components packaged in drums or totes.
-
Reduce footprint with a newly enhanced, more compact unit.
-
Increase operational efficiency by selecting up to 9 different control phases based on recipe requirements
-
No contamination of rinse tank by lance cleaning.