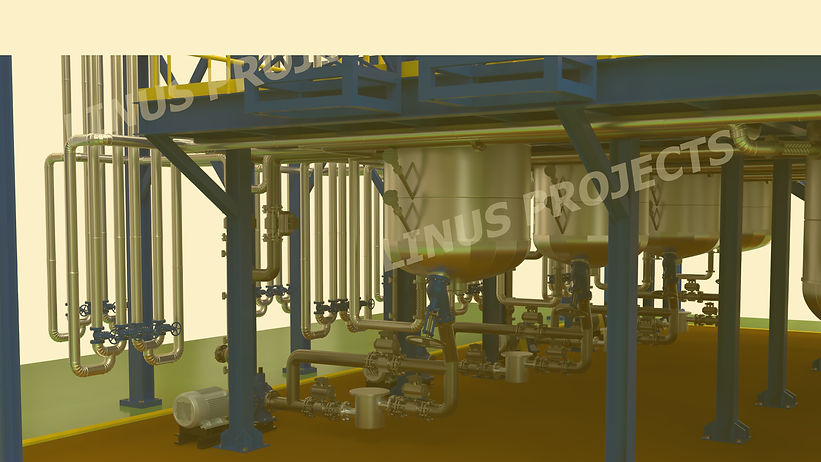
GREASE KETTLE
Linus Projects stands as a prominent Indian manufacturing company with an accomplished board-level management team boasting extensive expertise in engineering, design, and manufacturing. Our focus is on supplying carefully selected engineering products to meet the demand at the bottom line.
We specialize in designing, engineering, and manufacturing Double Motion Grease Kettles. These kettles play a pivotal role in the production of lubricating greases for various applications, including automobile, aircraft, railroad, and industrial uses.
Linus Projects offers three main types of grease kettles, also known as reactors:
1. Pressure Kettle (Reactor)
2. Non-Pressure Kettle (Reactor)
3. Bottom Conical Kettle (Reactor)
Our commitment to quality and innovation ensures that our grease kettles meet the diverse needs of industries requiring efficient and reliable solutions for grease production.
Pressure Kettle (Reactor):
Our Pressure Kettle features a robust design with a Double Motion Counter-Rotating Agitator Stirrer. This comprises a stationary-mounted drive assembly seamlessly integrated with the Grease Kettle Body, allowing for manual height adjustment. Located at the bottom of the kettle is a Flush Bottom Handwheel-operated Discharge/Sampling Valve for convenient access.
This Autoclave-type Pressurized Kettle boasts a 6 kg working capacity. The double motion counter-rotating agitator stirrer, reminiscent of a drill press arrangement, is a key component. It consists of a stationary-mounted drive assembly coupled with the grease kettle body, offering manual adjustment for height.
The kettle itself is constructed with two dishes and a shell, featuring a bottom dish equipped with a flush bottom discharge valve. The agitator assembly is intricately designed with a simplex system, where shafts with agitators effectively blend the grease and move the entire mass. Additionally, scrapers are strategically placed at the sides and bottom of the agitator assembly for thorough mixing.
Non Pressure kettle (Reactor):
The kettle consists of the bottom dish, shell & top lid. The bottom dish is fitted with a flush bottom discharge valve and one drain valve ball type for sample removing, testing, and checking. The agitator assembly consists of a simplex designed system where shafts fitted with agitators thoroughly blend the grease as well as move the entire mass. Scrapers are provided at the sides and bottom of the agitator assembly.
Bottom Conical Kettle (Reactor)
The Autoclave-Style Grease Kettle can be used for the complete grease manufacturing cycle - saponification, grease finishing, and cooling. However, The processing time is extended when compared to saponification being performed in a Linus Projects Grease Base Reactor. The Reactor with its jacketed vessel construction - jackets over both the shell and cone sections - and double-wall construction inner circulation tube offers a greatly increased surface area for transfer of heat to the soap. Coupled with this is the dramatically increased rate of product circulation brought about by the bottom propellor agitator that operates at full or half motor speed. This type of agitation/mixing action ensures a homogeneous soap base for transfer to the Grease Finishing-Cooling Kettle where the balance of oils and additives are charged and the final grease product is manufactured.
GREASE KETTLE
The Grease Kettle is an advanced pressure reactor designed for efficient grease production, particularly tailored for applications in the automobile, aircraft, railroad and industrial sectors. Specifically categorized as a Pressure Kettle (Reactor), this equipment is characterized by its cutting-edge features and meticulous design.
FEATURES:
-
Double Motion Counter-Rotating Agitator Stirrer: The Grease Kettle incorporates a sophisticated double motion counter-rotating agitator stirrer, featuring a stationary-mounted drive assembly seamlessly integrated with the adjustable Grease Kettle Body. This arrangement allows for precise manual adjustment in height, similar to a drill press.
-
Autoclave-Type Pressurized Design: With a 6 kg working capacity, the Grease Kettle is engineered with an autoclave-type pressurized system. This design ensures optimal performance and efficiency in the production of lubricating greases.
-
Flush Bottom Handwheel-Operated Valve: Positioned at the bottom of the kettle, a convenient Flush Bottom Handwheel-operated Discharge/Sampling Valve facilitates easy access for efficient discharge and sampling processes.
-
Robust Construction: The Grease Kettle is constructed with two dishes and a durable shell, featuring a bottom dish equipped with a flush bottom discharge valve. This robust construction ensures longevity and reliability in demanding industrial environments.
-
Innovative Agitator Assembly: The agitator assembly is designed with a simplex system, employing shafts fitted with agitators that thoroughly blend the grease and move the entire mass. Scrapers strategically placed at the sides and bottom of the agitator assembly enhance the mixing process.
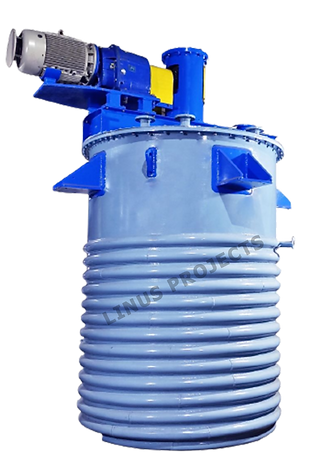
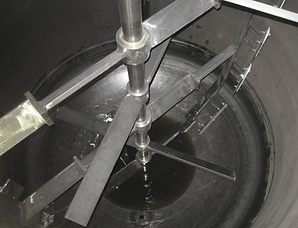
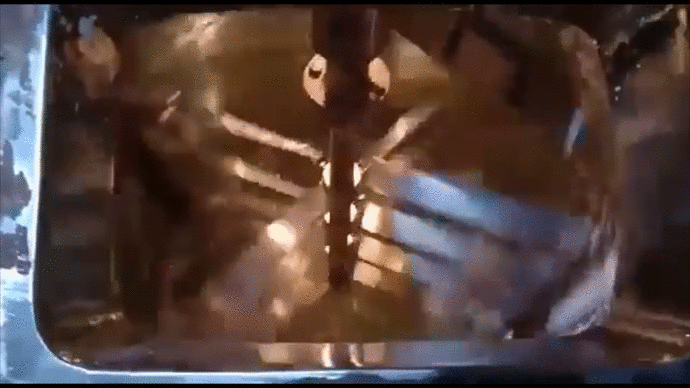
CONTRA ROTARY BLADE
A Grease Toothed Colloid Mill is a specialized machinery designed for the efficient processing of grease and lubricants. This innovative mill employs a unique toothed rotor and stator arrangement to effectively emulsify, homogenize, and disperse grease particles, resulting in a smooth and consistent product.
FEATURES:
-
The Contra Rotary Blade operates on a contra-rotary principle, where two blades rotate in opposite directions. This innovative mechanism facilitates a high level of turbulence and agitation within the mixing vessel, ensuring a consistent and uniform distribution of ingredients.
-
The contra-rotary motion of the blades ensures a thorough homogenization of grease components. This results in a well-blended and high-quality product, meeting the stringent standards of the lubricant industry.
-
The blade's design allows for customization based on specific grease formulations and production requirements. This adaptability ensures optimal performance across a diverse range of applications and formulations.
-
Crafted from high-quality materials, the Contra Rotary Blade boasts durability and resilience. Its robust construction enables it to withstand the rigors of continuous mixing operations, contributing to a long service life.
-
The blade's design facilitates easy maintenance, with accessible components that can be inspected and serviced efficiently. This feature minimizes downtime and ensures continuous, reliable operation.
-
The Contra Rotary Blade is versatile in its application, suitable for use in various mixing vessels and equipment. Its adaptability makes it an ideal choice for different scales of grease production.
The Grease Kettle, with its advanced features and design, finds versatile applications across various industrial sectors. Some key applications of Grease Kettles include:
-
Automobile Industry: Grease Kettles are extensively used in the automobile industry for the production of lubricating greases. These greases are vital for ensuring smooth operation and reduced friction in automotive components such as bearings, joints, and gears.
-
Aircraft Maintenance: In the aviation sector, Grease Kettles play a crucial role in producing high-performance lubricating greases that are essential for the maintenance and proper functioning of aircraft components, including landing gear, engines, and control systems.
-
Railroad Maintenance: Grease is essential for the effective lubrication of railroad components, including rail joints, wheel bearings, and switches. Grease Kettles are employed in the railroad industry to produce the specialized lubricants needed for smooth and safe railway operations.
-
Industrial Manufacturing: Grease Kettles are widely utilized in general industrial manufacturing where lubricating greases are required for the efficient operation of machinery and equipment. This includes applications in manufacturing plants, processing facilities, and other industrial settings.
-
Energy Sector: Grease is utilized in the energy sector to lubricate various components of machinery used in power generation, including turbines, generators, and bearings. Grease Kettles play a role in producing greases tailored to the specific requirements of the energy industry.
-
Heavy Machinery: Grease is essential for the proper functioning of heavy machinery in construction, mining, and other sectors. Grease Kettles are employed to manufacture greases that can withstand the harsh operating conditions of heavy-duty equipment.
-
General Lubrication: Grease Kettles are used in applications where general lubrication is required, such as in manufacturing processes, industrial maintenance, and equipment servicing.
In summary, Grease Kettles have diverse applications across industries that rely on effective lubrication for the smooth and efficient operation of machinery and components. Their versatility and ability to produce tailored lubricating greases make them integral to various sectors where friction reduction and component longevity are critical.